Optimizing Solar Array Performance Through Flexible Braided Grounding Conductors
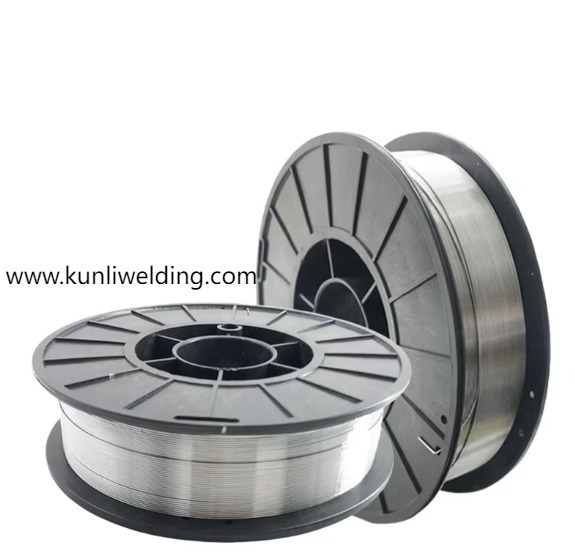
Amid the surge in clean power investments, Aluminum Braided Wire Manufacturers are stepping up to supply essential components for renewable energy infrastructure. As wind farms expand offshore and solar arrays stretch across deserts and rooftops, the demand for durable braided wiring solutions has never been higher. These specialized products enable secure cable connections and effective grounding systems that support uninterrupted energy flow and safeguard critical equipment against electrical faults.
In wind energy installations, braided wire finds its niche in grounding towers and turbine nacelles. High strength braid assemblies bridge the gap between metal structures and earthing grids, channeling stray currents safely into the ground. This capability not only protects sensitive control electronics but also reduces corrosion risks at connection points exposed to harsh marine environments. By maintaining consistent conductivity under mechanical stress, braided solutions ensure that wind turbines continue spinning reliably, even in fluctuating weather conditions.
Solar farms also benefit from braided grounding conductors linking panel frames and mounting racks to central earthing networks. With installations covering vast areas, maintaining uniform potential across the array is essential to avoid performance losses and lightning damage. Braided conductors flex under thermal expansion and contraction, preventing loosening or fatigue at termination points. Their pliable nature simplifies installation across uneven terrain, speeding up site commissioning and minimizing labor costs without compromising long term resilience.
Beyond grounding, braided assemblies serve as flexible interconnects in power conversion units, where inverters and transformers require vibration resistant wiring. As renewable energy projects push into hybrid microgrid solutions, braided wire helps integrate battery storage systems and monitoring equipment. The combination of conductivity and flexibility supports rapid maintenance cycles, enabling field engineers to replace sections without dismantling entire harnesses. This modular approach aligns with agile operations that prioritize uptime in mission critical applications.
Recent policy initiatives aimed at modernizing electrical grids have spurred interest in incorporating braided wiring into utility scale energy management centers. Within control rooms and substation shelters, braided bus connectors unite power electronics with backup systems, providing low impedance pathways for fault currents. By reducing electrical noise and improving grounding performance, these wiring assemblies contribute to grid stability and protect sensitive digital relays from transient surges.
Sustainability considerations further underscore the appeal of aluminum braided wire. Compared with traditional copper alternatives, aluminum offers a lighter weight and lower material footprint without sacrificing conductivity when properly engineered. Recycling programs reclaim scrap wire from manufacturing processes and end of life installations, closing the loop on material use and supporting circular economy goals. Buyers focused on green credentials appreciate suppliers that document environmental practices and use renewable energy in their own operations.
Innovation in alloy composition and braiding techniques continues to enhance product performance. Real time monitoring systems can track tension and strand alignment during production, ensuring each spool meets exacting specifications. Some manufacturers offer custom braid patterns that balance flexibility with tensile strength, tailored to specific project requirements. This level of customization gives engineers the freedom to optimize their designs for space constrained installations or extreme temperature ranges.
Risk mitigation remains a priority for project planners sourcing braided wire solutions. Thorough testing under simulated field conditions—covering salt spray exposure and cyclic bending—provides confidence that components will endure throughout the asset lifecycle. Digital traceability systems link each batch to production data and quality records, allowing buyers to trace performance history and streamline maintenance schedules.
As renewable energy systems mature and diversify, the role of Aluminum Braided Wire Manufacturers will continue to expand. By combining engineering expertise with sustainable production and robust quality assurance, these suppliers support the transition to a cleaner power mix and help stakeholders meet ambitious climate objectives.For access to a comprehensive portfolio of braided wiring solutions and expert technical guidance, explore our offerings at www.kunliwelding.com/product/ .
- Art
- Causes
- Crafts
- Dance
- Drinks
- Film
- Fitness
- Food
- Juegos
- Gardening
- Health
- Home
- Literature
- Music
- Networking
- Other
- Party
- Religion
- Shopping
- Sports
- Theater
- Wellness