Why Aluminum Roller Customization Matters in Precision Machinery
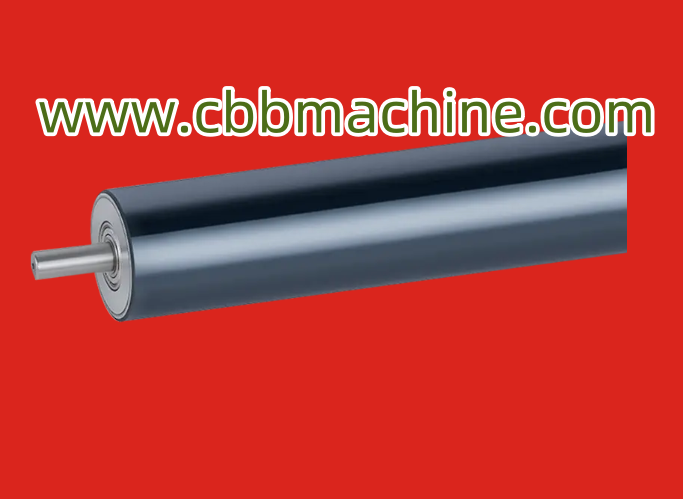
Precision Performance with the Right Aluminum Roller
An Aluminum Roller is a critical component in modern industrial machinery, playing a key role in applications where lightweight strength, corrosion resistance, and smooth surface operation are essential. Whether in film production, paper handling, textile processing, or packaging lines, these rollers contribute significantly to the efficiency and precision of moving or processing materials.
Aluminum is known for its favorable properties in engineering and mechanical design. When crafted into rollers, this material provides a durable, lightweight alternative to heavier steel components, enabling faster speeds and reduced wear on surrounding systems. Additionally, aluminum's excellent resistance to corrosion makes these rollers ideal for environments where moisture or chemicals are present.
Core Benefits of Using Aluminum Rollers
One of the most appealing characteristics of aluminum rollers is their weight advantage. In systems that rely on rotation or continuous movement, minimizing mass reduces strain on motors, bearings, and shafts. This translates to energy savings and longer machine life. The use of aluminum can also help improve balance and responsiveness in high-speed applications, allowing for finer control and less vibration.
In terms of surface properties, aluminum offers versatility. Rollers can be anodized, polished, or coated to suit various application needs. For example, in film or foil processing, a polished aluminum roller ensures minimal surface friction and reduces the risk of material wrinkling or scratching.
Thermal conductivity is another reason aluminum is widely chosen. In applications where temperature regulation is necessary, such as in laminating or heat sealing equipment, aluminum rollers can dissipate heat efficiently and support consistent process temperatures.
Design Considerations and Customization
Selecting the right aluminum roller involves more than just choosing the appropriate material. Engineers and machine operators need to consider factors such as roller diameter, wall thickness, surface treatment, and balance requirements. In high-precision or dynamic environments, even small variations in roller alignment or roundness can cause significant performance issues.
Custom rollers can be fabricated to meet specific industrial needs. Some may require hollow aluminum rollers to reduce inertia, while others benefit from reinforced ends or shafts to handle higher torque. Additionally, rollers may be grooved, knurled, or coated with rubber or silicone depending on the type of material they interact with.
This level of customization allows manufacturers to fine-tune their machinery for maximum productivity. Working with a supplier that understands these variables ensures that each aluminum roller performs reliably in its intended function.
Applications Across Multiple Industries
Aluminum rollers are not confined to one sector. Their widespread use includes:
Printing and Packaging: For feeding films, labels, and flexible packaging materials at high speeds.
Paper and Tissue Production: For smooth conveyance and wrinkle-free handling of thin materials.
Textile Industry: Where light pressure and smooth surface contact are needed for delicate fabrics.
Converting Processes: In applications like slitting and rewinding, aluminum rollers support stable material movement.
The adaptability of aluminum as a roller material makes it a practical choice across all of these areas. Industries that require precise material handling and consistent quality benefit significantly from implementing aluminum roller systems.
Maintaining Roller Quality for Long-Term Use
Like all mechanical parts, aluminum rollers require regular inspection and maintenance to retain performance. Factors such as debris buildup, surface wear, or imbalance can impact the roller's function. Cleaning with non-abrasive materials and monitoring for signs of wear or damage can help extend the roller's operational life.
Additionally, ensuring proper installation and alignment in machinery prevents unnecessary stress and helps maintain accuracy during operation. In high-speed or heat-exposed environments, checking for warping or surface degradation is especially important.
Conclusion
Aluminum rollers offer a valuable combination of strength, lightness, and corrosion resistance that supports a wide range of industrial processes. Their ability to be customized, along with reliable performance in both standard and specialized settings, makes them a smart investment for manufacturers aiming to optimize machinery performance. With the right aluminum roller design and maintenance plan, industries can expect smoother operations and longer equipment lifespan.
- Art
- Causes
- Crafts
- Dance
- Drinks
- Film
- Fitness
- Food
- Spellen
- Gardening
- Health
- Home
- Literature
- Music
- Networking
- Other
- Party
- Religion
- Shopping
- Sports
- Theater
- Wellness