Smart Clamping Solutions: Bridging Accuracy and Adaptability
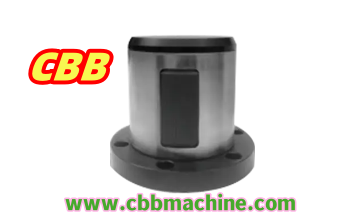
Mechanical Expand Chuck :In today’s fast-paced manufacturing landscape, achieving flawless precision while maintaining operational agility is a constant challenge. Enter advanced clamping systems—innovative solutions designed to address inefficiencies in toolholding, reduce downtime, and elevate machining accuracy. Among these breakthroughs, radial expansion-based clamping mechanisms have emerged as a cornerstone for industries where performance and reliability are non-negotiable.
Core Innovation: How It Works Radial expansion technology utilizes a mechanically driven mechanism to apply uniform pressure around a tool or workpiece. This method ensures a secure, vibration-free grip, eliminating the misalignment and slippage common in traditional collet or hydraulic systems. By maintaining consistent concentricity, these systems enhance cutting precision, reduce tool wear, and improve surface finishes—critical for high-tolerance applications.
Constructed from high-strength alloys and subjected to rigorous heat treatments, these clamping units resist deformation under extreme operational stresses. Advanced coatings further protect against corrosion and wear, ensuring longevity in demanding environments such as aerospace machining or automotive production lines.
Applications That Demand Perfection
Aerospace: Machining turbine blades and structural components requiring tolerances under 10 microns.
Automotive: High-volume production of transmission parts and electric vehicle components with rapid tool-swap capabilities.
Medical Technology: Fabricating surgical instruments and implants where surface integrity is paramount.
Electronics: Securing micro-tools for precision engraving and circuit board manufacturing.
Energy Sector: Crafting wind turbine gears and oil-drilling equipment with unwavering stability.
Why Industry Leaders Are Adopting This Technology
Zero-Play Design: Ensures tools remain rigidly fixed, even during aggressive machining cycles.
Rapid Tool Changes: Reduces setup time by up to 50%, boosting production throughput.
Cost Efficiency: Extended tool lifespan and reduced scrap rates lower operational expenses.
Versatility: Compatible with diverse tool sizes, minimizing the need for multiple adapters.
Sustainability: Energy-efficient operation supports eco-friendly manufacturing initiatives.
Proven Impact Across Global Industries Manufacturers worldwide report transformative results after integrating radial expansion clamping systems. For example, a leading aerospace supplier reduced cycle times by 18% while achieving 99.9% first-pass yield rates. Similarly, an automotive plant slashed tooling-related downtime by 40%, translating to significant annual cost savings.
Compliance with ISO 15407 and industry-specific certifications underscores their reliability. Furthermore, seamless integration with CNC machines and lathes allows businesses to upgrade existing setups without costly overhauls, ensuring minimal disruption to workflows.
Sustainability and Future-Forward Innovation As industries prioritize greener practices, these clamping systems contribute by minimizing material waste and energy consumption. Durable construction reduces replacement frequency, while emerging smart features—such as IoT-enabled force monitoring—pave the way for predictive maintenance and real-time process optimization. Future advancements may include AI-driven adjustments to adapt to dynamic machining conditions autonomously.
Conclusion Radial expansion-based clamping systems are redefining the benchmarks for precision, efficiency, and sustainability in modern manufacturing. By solving persistent challenges in toolholding, they empower businesses to achieve unparalleled quality and productivity. For enterprises aiming to lead in competitive markets, adopting this technology is a strategic investment in operational excellence.
Explore how these innovative solutions can transform your production processes with CBB Machine’s cutting-edge engineering expertise. Renowned for delivering robust, future-ready toolholding systems, their offerings are trusted by global industry leaders to meet the demands of tomorrow’s manufacturing challenges.www.cbbmachine.com
- Art
- Causes
- Crafts
- Dance
- Drinks
- Film
- Fitness
- Food
- Παιχνίδια
- Gardening
- Health
- Κεντρική Σελίδα
- Literature
- Music
- Networking
- άλλο
- Party
- Religion
- Shopping
- Sports
- Theater
- Wellness